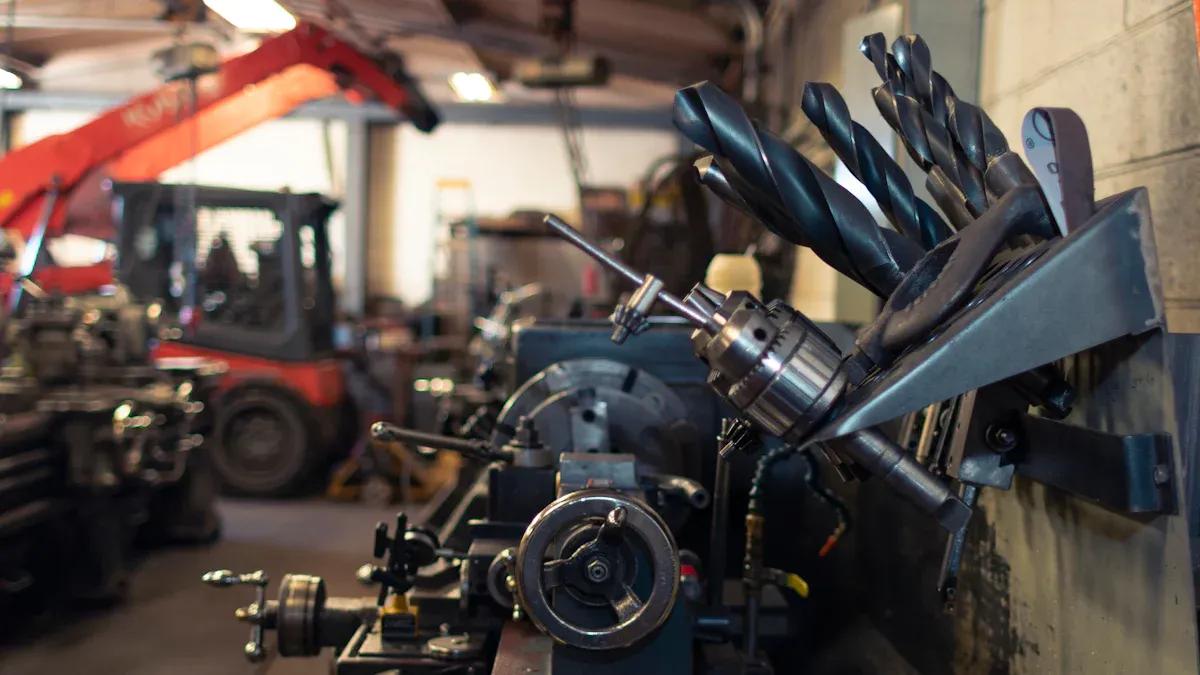
The bottom feed roller and shaft play a pivotal role in ensuring smooth machine operation. These components directly influence performance, durability, and precision. Selecting the wrong parts can lead to inefficiency, costly repairs, or even machine failure. This guide empowers readers to make informed decisions, safeguarding their equipment and optimizing productivity.
Key Takeaways
● Picking the right bottom feed roller and shaft is important for smooth machine work. It helps avoid problems and expensive fixes.
● Make sure they match your machine's needs. Check motor details, sizes, and how they work to fit the parts correctly.
● Cleaning and oiling them often makes them last longer. Plan check-ups to find problems early and stop delays.
Why Choosing the Right Bottom Feed Roller and Shaft Matters
Role in Machine Operation
The bottom feed roller and shaft serve as critical components in machine operation. Their primary function involves material handling, ensuring smooth feeding and processing. For instance, the lower feed flattening roller grabs and flattens materials like straw, while the upper feed flattening roller works in tandem to maintain precision. The movable shaft adjusts conveyor chain plate tension, optimizing the feeding mechanism. These components collectively ensure seamless operation, reducing the risk of material jams or uneven processing.
Component |
Function |
Lower feed flattening roller | Grabs and flattens the straw, essential for effective material processing. |
Upper feed flattening roller | Works in conjunction with the lower roller to ensure proper material flattening. |
Movable shaft | Allows adjustment of the conveyor chain plate tension, optimizing the feeding mechanism. |
Sliding groove | Facilitates the adjustment of the gap between rollers based on material properties. |
Impact on Efficiency and Productivity
Selecting the correct bottom feed roller and shaft directly impacts machine efficiency and productivity. Properly matched components reduce production downtime and enhance throughput. For example, the feed flattening roller transmits power through gear and chain transmission, ensuring consistent material handling. Metrics like mean time to repair (MTTR) highlight the importance of reliable components, as faster repairs minimize downtime and associated costs.
Metric |
Description |
Production Downtime | Measures the time when production is halted, impacting overall efficiency and costs. |
Throughput | Indicates the amount of product produced in a given timeframe, reflecting productivity levels. |
Mean Time to Repair (MTTR) | Assesses the average time taken to repair equipment, crucial for minimizing downtime and costs. |
Risks of Using Incorrect Components
Using incorrect bottom feed rollers and shafts can lead to significant risks. Misaligned or incompatible parts may cause material jams, uneven feeding, or excessive wear on other machine components. These issues increase production downtime and repair costs. Additionally, improper adjustments to the sliding groove or movable shaft can compromise feeding accuracy, reducing overall productivity. Selecting high-quality, compatible components mitigates these risks, ensuring long-term operational reliability.
● The lower feed flattening roller shaft transmits power through gear and chain transmission.
● The feed flattening roller's key task is to grasp and flatten the straw, ensuring effective operation.
Key Factors to Consider When Selecting a Bottom Feed Roller and Shaft
Compatibility with Machine Specifications
Ensuring compatibility with machine specifications is the first step in selecting the right bottom feed roller and shaft. Each machine has unique requirements, including motor specifications, physical dimensions, and operational parameters. For instance, motor voltage, torque ratings, and power consumption must align with the roller's capabilities. Additionally, physical dimensions such as the roller's size and the conveyor system's measurements ensure seamless integration.
Specification Type |
Details |
Motor Specifications | Voltage, power consumption, and torque ratings for various rollers. |
Physical Dimensions | Diagrams and measurements for compatibility with conveyor systems. |
Operational Temperatures | Guidelines for temperature ranges for different roller models. |
Load Capacities | Maximum load each roller can handle for application needs. |
Speed Ranges | Data on adjustable speed ranges for precise control over material flow. |
Matching these specifications minimizes downtime and ensures optimal performance.
Material Options and Their Benefits
The material of the bottom feed roller and shaft significantly impacts durability and performance. Urethane rollers, for example, offer superior abrasion resistance compared to rubber, reducing the frequency of replacements. Their chemical resistance makes them ideal for environments exposed to solvents, while their durability ensures a longer lifespan in demanding applications. In the automotive industry, urethane rollers reduce wear and tear, enhancing the lifespan of parts. Additionally, they prevent slippage and scuffing, making them suitable for delicate operations like food processing. Selecting the right material ensures cost savings and operational efficiency.
Size, Weight, and Dimensions
Size, weight, and dimensions play a critical role in ensuring the roller and shaft fit seamlessly into the machine. Standards such as ISO Tolerance Classes and Recommended Fits provide guidelines for selecting the correct dimensions. For example, cylindrical shaft seats require specific tolerance classes based on rotation conditions and bearing types. Proper sizing prevents misalignment, reduces wear, and ensures smooth operation.
Specification Type |
Description |
ISO Tolerance Classes | Defined in ISO 2861 and ISO 286-2, indicating fundamental deviation and tolerance quality. |
Recommended Fits | Tables provide recommendations for shaft and housing tolerances for normal conditions, with adjustments for specific requirements. |
Tolerance Classes for Cylindrical Shaft Seats | Lists conditions of rotation, bearing types, shaft diameters, and corresponding tolerance classes. |
Performance and Application Requirements
Performance evaluation is essential to determine the suitability of a bottom feed roller and shaft for specific applications. Rolling bearings, for instance, minimize friction and ensure high accuracy. Environmental factors, load intensity, and wear can affect performance, making it crucial to test components under various conditions. High-quality rollers and shafts maintain low power loss and consistent performance, ensuring reliability across industries. Selecting components that meet application requirements enhances productivity and reduces maintenance costs.
Types of Bottom Feed Rollers and Shafts
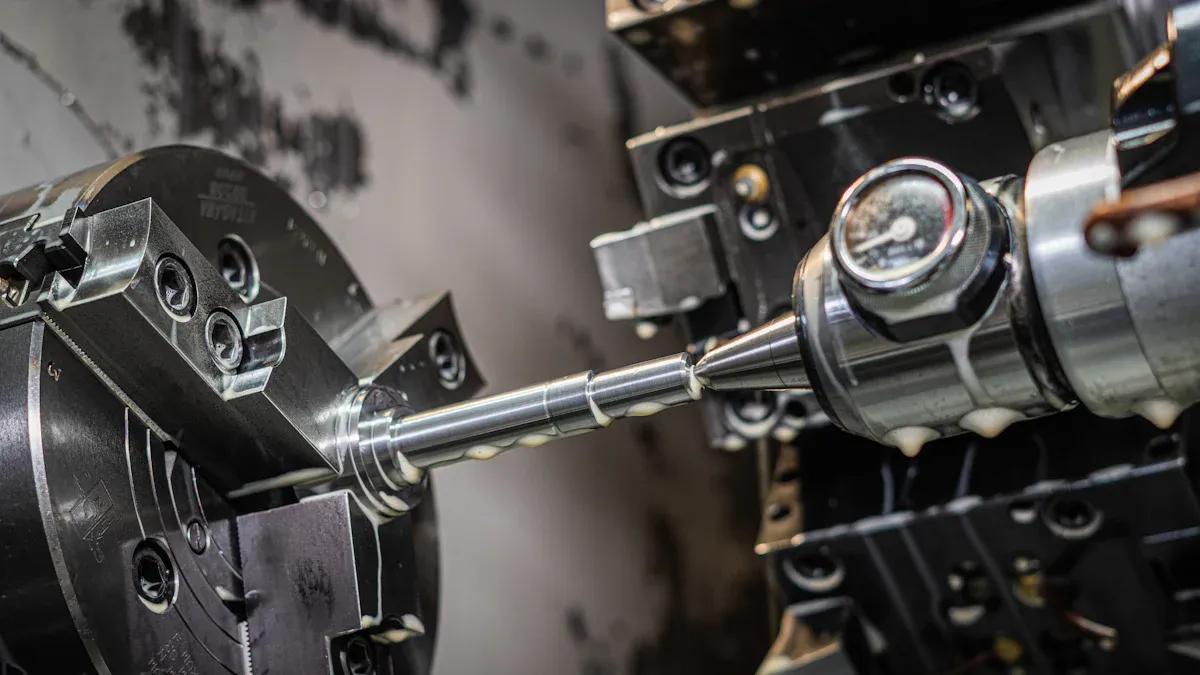
Common Roller Types and Their Uses
Different types of rollers serve specific purposes in various industries. Each type is designed to optimize machine performance and ensure smooth material handling.
● Smooth Wheeled Rollers: Ideal for compacting asphalt layers, commonly used in road construction.
● Pneumatic Tired Rollers: Suitable for compacting fine-grained soils and asphalt, offering versatility in construction projects.
● Straight Rollers: Versatile components used with or without conveyor belts for general material handling.
● Crowned Rollers: Essential for keeping long sheets of material centered during movement, ensuring precision.
● Grooved Rollers: Designed to center workpieces along conveyor belts, reducing misalignment risks.
● Knurled Rollers: Provide enhanced friction for better grip, making them suitable for delicate applications.
Type of Roller |
Description |
Application |
Conveyor Rollers | Facilitate smooth movement of materials in conveyor systems. | Manufacturing plants and distribution centers. |
Heavy Duty Rollers | Withstand high loads for moving heavy materials. | Mining and construction industries. |
Drive Rollers | Motorized rollers providing driving force. | Automated assembly lines and material handling. |
Guide Rollers | Prevent lateral movement of materials. | Printing presses and material feed systems. |
Idler Rollers | Support material weight without driving it. | Bulk material handling applications. |
Shaft Designs and Applications
Shaft designs vary based on their intended applications, with each characteristic influencing performance.
Shaft Characteristic |
Description |
Impact on Performance |
Flex | Determines the shaft's bending capability. | Affects precision; excessive flex may reduce control. |
Weight | Ranges from 45g to 137g. | Heavier shafts enhance stability; lighter ones boost speed. |
Torque | Refers to the twisting during operation. | Lower torque improves control; higher torque enhances flexibility. |
Kick Point | Indicates the location of maximum bend. | Influences trajectory; low kick points launch higher. |
For example, shafts with higher torque are preferred in applications requiring greater flexibility, while heavier shafts are ideal for stability in high-load environments. Selecting the right shaft design ensures optimal performance and durability.
Material Comparisons: Steel, Rubber, and Composite
The material of a bottom feed roller and shaft determines its durability, resistance, and suitability for specific tasks.
● Steel: Offers exceptional strength and durability, making it ideal for heavy-duty applications like mining and construction.
● Rubber: Provides excellent grip and shock absorption, suitable for delicate operations such as food processing.
● Composite: Combines lightweight properties with high resistance to wear, ensuring longevity in demanding environments.
Each material has unique advantages. Steel excels in high-load scenarios, rubber minimizes damage to sensitive materials, and composite materials balance strength and weight for versatile applications. Selecting the appropriate material enhances the efficiency and lifespan of the bottom feed roller and shaft.
How to Choose the Best Bottom Feed Roller and Shaft for Your Machine
Evaluating Machine Specifications
Evaluating machine specifications is the foundation for selecting the right bottom feed roller and shaft. A detailed analysis ensures compatibility and optimal performance. Techniques such as model-driven approaches use mathematical models to predict how components will perform under specific conditions. Data-driven methods rely on historical data to assess performance trends, while deep learning leverages neural networks for complex evaluations.
Method Type |
Description |
Model-driven | Approaches that rely on mathematical models to predict performance. |
Data-driven | Techniques that utilize historical data to inform performance evaluations. |
Deep learning | Advanced methods that leverage neural networks for complex performance analysis. |
These techniques help identify the most suitable components, ensuring seamless integration and enhanced machine efficiency.
Consulting Manufacturer Guidelines
Manufacturer guidelines provide critical insights into component compatibility and performance. These documents outline specifications such as load capacities, operational temperatures, and speed ranges. Consulting these guidelines minimizes the risk of selecting incompatible parts. Manufacturers often include recommendations for maintenance practices, ensuring the longevity of the bottom feed roller and shaft. Adhering to these guidelines enhances operational reliability and reduces downtime.
Testing and Practical Evaluation Tips
Testing components under real-world conditions is essential for verifying their suitability. Practical evaluation involves assessing factors like load handling, wear resistance, and operational efficiency. For instance, testing rollers in varying environmental conditions ensures they meet application-specific requirements. Observing performance metrics such as power loss and material handling precision provides valuable insights. Regular testing also identifies potential issues early, preventing costly repairs.
Real-World Examples of Selection Scenarios
Real-world applications highlight the importance of selecting the right bottom feed roller and shaft. In automotive assembly lines, steel rollers facilitate the movement of parts through production stages. Stainless steel rollers are preferred in food and beverage processing for their corrosion resistance and hygiene. Durable steel rollers ensure reliable luggage transport in airport baggage handling systems. Heavy-duty rollers withstand harsh conditions in mining operations, while precision-engineered rollers support cleanroom environments in pharmaceutical manufacturing. These examples demonstrate how tailored selections optimize performance across industries.
Maintenance Tips for Bottom Feed Roller and Shaft Longevity
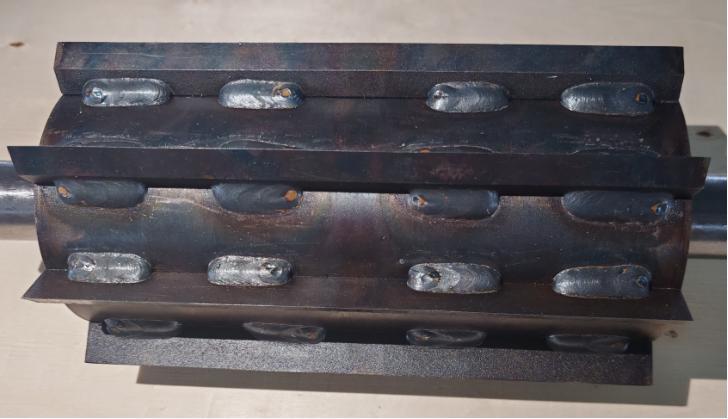
Regular Inspection and Cleaning Practices
Regular maintenance ensures the longevity and efficiency of the bottom feed roller and shaft. A structured inspection routine minimizes wear and prevents unexpected failures. Follow these steps to maintain optimal performance:
1.Clean rollers and brackets regularly to remove dust and debris that may impair functionality.
2.Lubricate bearings and moving parts periodically to reduce friction and wear.
3.Inspect roller alignment and adjust brackets to prevent misalignment-related damage.
4.Examine rollers and brackets for visible signs of wear or damage. Replace components as necessary.
5.Tighten all fasteners to prevent loosening caused by vibrations.
6.Monitor load capacities to avoid overloading, which can stress the system.
7.Investigate unusual noises promptly to identify potential issues.
8.Replace damaged rollers immediately to prevent further harm to the conveyor system.
9.Use compatible parts to ensure efficiency and reliability.
10.Schedule routine inspections to detect issues early.
11.Train personnel on proper maintenance practices.
12.Maintain detailed records of inspections and repairs for future reference.
Lubrication and Wear Prevention
Proper lubrication plays a vital role in reducing wear and extending the lifespan of the bottom feed roller and shaft. Lubrication minimizes friction between moving parts, flushes out debris, and ensures smooth engagement with sprockets. Studies show that adequate lubrication can extend chain life by up to 100 times. It also prevents erratic motion and excessive friction, which often lead to premature component failure. Regularly applying the correct lubricant ensures consistent performance and reduces maintenance costs.
Identifying Signs of Wear and Replacement Timing
Monitoring vibration levels helps identify wear and determine the optimal time for replacement. Key indicators include:
Indicator |
Description |
RMS | Measures overall vibration levels. |
Peak Value | Tracks maximum vibration amplitude, highlighting performance spikes. |
Average Amplitude | Shows general wear trends over time. |
Peak Factor | Indicates the severity of vibration spikes by comparing peak values to RMS. |
Kurtosis | Detects irregularities in vibration signal distribution. |
Performance remains stable for the first 80 hours of operation. However, wear increases significantly after 116 hours, signaling the need for replacement. Regular monitoring ensures timely action, preventing costly downtime.
Best Practices for Extending Component Life
Adopting best practices enhances the durability of the bottom feed roller and shaft. Consider the following guidelines:
● Maintain shaft concentricity within 0.025 mm to prevent misalignment.
● Ensure mechanical seal faces remain square to the shaft.
● Use steady bearings near the seal to minimize rocking and swaying.
● Keep shaft overhang small or use a thicker shaft for added stability.
● Align shafts accurately at operating temperatures.
● Maintain a clean flushing product or barrier fluid for seal faces.
Implementing these measures ensures long-term reliability and reduces the frequency of replacements.
Selecting the right bottom feed roller and shaft ensures optimal machine performance and long-term reliability. Key considerations include compatibility, material selection, size, and application-specific needs. Consulting manufacturers or professionals provides valuable guidance when uncertainties arise. Regular maintenance, such as cleaning and lubrication, reduces wear and extends component life, ensuring cost efficiency over time.
FAQ
What is the most important factor when selecting a bottom feed roller and shaft?
Compatibility with machine specifications is crucial. Ensuring proper dimensions, material, and performance alignment prevents inefficiencies and enhances operational reliability.
Tip: Always consult manufacturer guidelines for precise compatibility details.
How often should bottom feed rollers and shafts undergo maintenance?
Perform maintenance every 100 operational hours or monthly, whichever comes first. Regular inspections and lubrication extend component life and prevent unexpected failures.
Can Ningbo Jiangbei XinYe Metal Works Co., Ltd. provide custom bottom feed rollers and shafts?
Yes, XINYE offers OEM and ODM services. Their expertise ensures tailored solutions for unique machine requirements across industries like automotive, aerospace, and food processing. Contact XINYE's technical team for personalized assistance.
Post time: Mar-13-2025